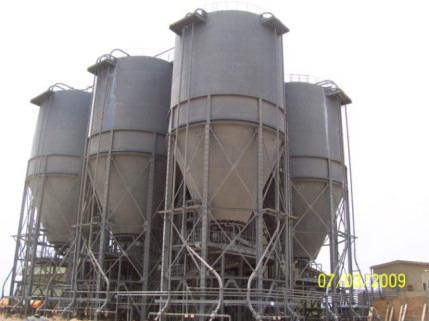
Cement Bagging Plant (Ghana)
For optimal protection, ZINGA should be applied in two layers of 60 or 90 µm DFT each.
ZINGA and the topcoats work in harmony to extend the lifetime of the system. As the ZINGA layer will not begin to sacrifice itself until the topcoat is breached, the original zinc thickness is maintained whilst affording the topcoat protection from under-creep and blistering.
In a duplex and triplex system (Active + Passive), ZINGA should be applied in 1 layer of min. 60 to 80 µm DFT.
For more information and application instructions, see ‘Overcoating ZINGA’.
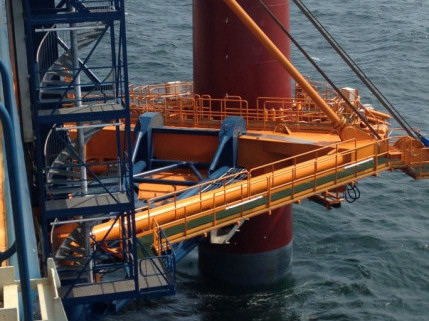
Wind Mills (Belgium)
At 30-40 µm DFT, ZINGA can be used as a shop primer. The big benefit is found in the fact that the steel structures do not require reblasting before coating if ZINGA is applied as a shop primer. The steel structure can be overcoated with ZINGA to obtain a cathodic protection or with any other paint without the need for reblasting!
Zinganised steel structures can be welded and bent during assembly.
This method is probably the most common use of ZINGA as it requires the simplest surface preparation. ZINGA’s mechanism of protection is so similar to conventional galvanizing that they work in complete unison, as they are merely different forms of zinc. Rather than replacing galvanized assets, structures can simply have their protection “re-charged” by applying ZINGA to the rough surface of the old galvanizing after appropriate decontamination of the surface and removal of the salts.
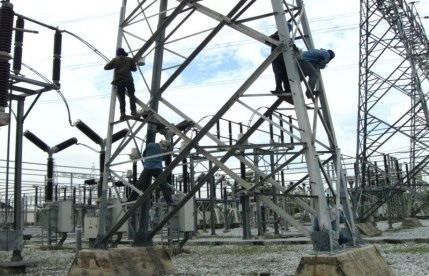
Pylons (Thailand)
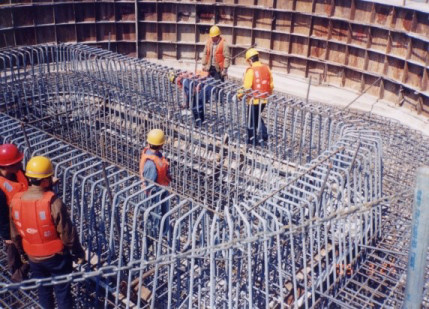
Rebars in Bridge (China)
Independent laboratory testing performed by multiple institutes has proven ZINGA can guarantee twice the corrosion protection compared to that of galvanised or epoxy coated rebars.